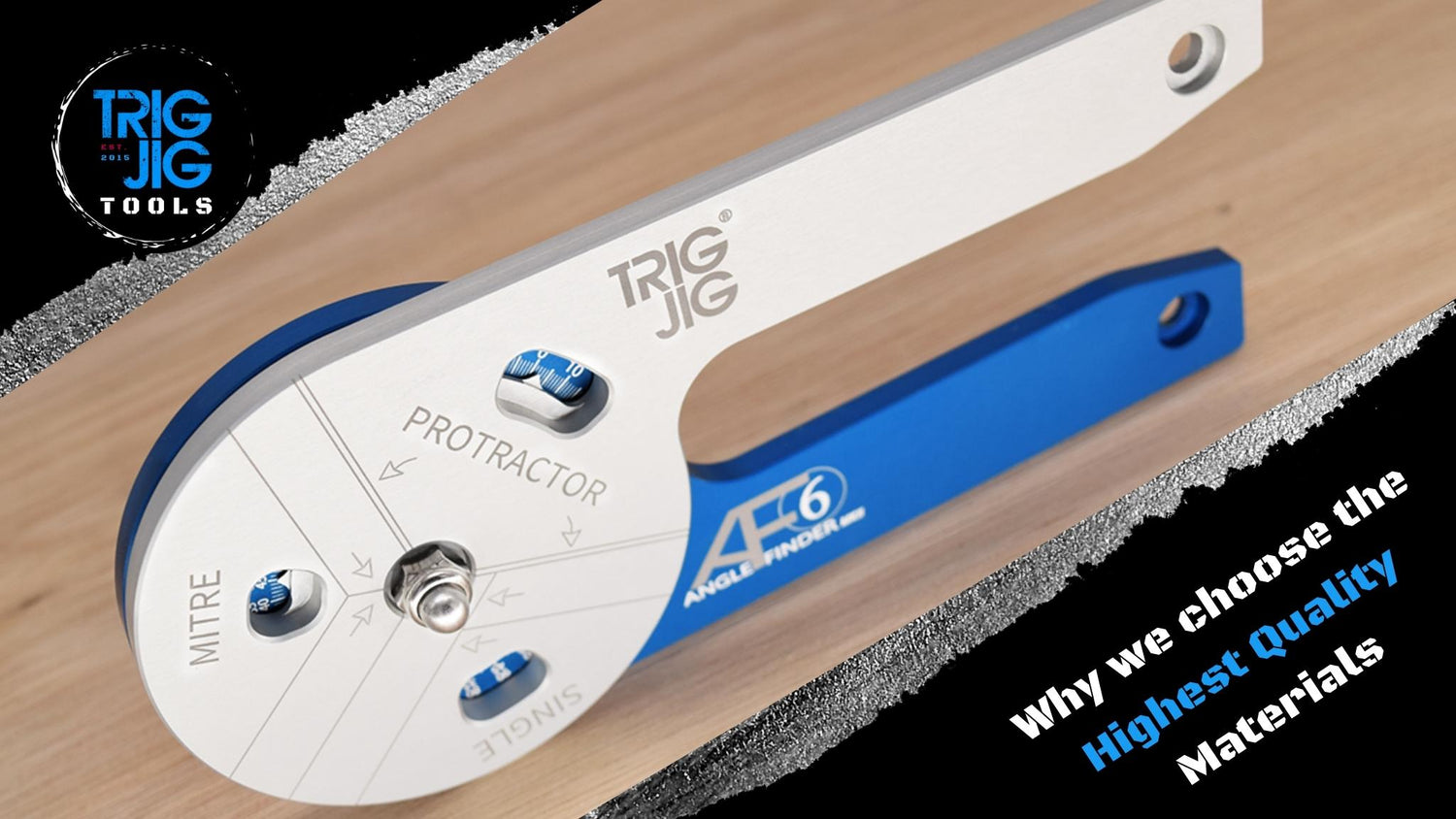
Quality materials for our hand tools
Quality Materials
In this TrigJig talk post, we're looking at the next item on the list: Why we choose the Highest Quality Materials.
One of the biggest challenges in making high quality hand tools is choosing the right raw materials. There is ALWAYS a tradeoff when it comes to this decision. The first thing we decided was that we should avoid using plastic as it nearly always feels naff and flimsy. Two things, that TrigJig Tools, are definitely not! That’s not to say plastic doesn’t have its place in tool manufacturing. Most power tools benefit greatly from the lightweight and shock resistant properties that specialist plastics offer. But for hand tools, plastic rarely wins and as we make small batches of tools, the mass manufacturing benefits of plastic doesn’t apply to us.
We knew we wanted to focus on metals as our dominant material and promptly invested in the machinery to enable us to work it. We tested dozens of different grades of steel, stainless steel, spring steel, brass, 5000, 6000 and 7000 series aluminium too. What we quickly realised was that the best materials for a given tool were not necessarily the best for another.

An example of this is our Carpenter Squares. For this we used T6 6082 aluminium, and we use the same aluminium for our angle finders. However, the plate we use for the angle finders tends to bow when machining on the long lengths of the carpenter squares due to the limited securing holes. We could solve this of course by drilling more work holding holes in the square. But that massively impacts the appearance. Instead we opted for case aluminium for the Carpenter Squares, despite it almost doubling the cost.

And then there’s the anodising. The Angle Finder parts are quite happy to be processed through the anodising plant to 15 microns thick and are usually uniform in colour. The cast CS300 on the other hand requires a lot more care due to its more porous finish.
Then there’s the big issue. The first reason why our tools are more expensive than those manufactured in the far east. We source our aluminium from European suppliers, and boy is this expensive. The raw materials alone in most of our tools costs more than the finished article of a mass produced alternative. In 2021 we ordered some aluminium from a supplier we weren’t familiar with for a surprisingly marginal increase considering the time. This was the height of the Covid pandemic and materials were becoming scarce.

When the stock arrived, the CNC machining centre suffered several tool breakages due to chip weld (where the cutting tool heats the material so much through friction that they glue themselves together) and during the anodising process we noticed we couldn’t get a uniform thickness on the surface at all. It caused 2 days of lost time and wastage and when I looked back through the material conformity documents, I realised it had originated from East China! Frustratingly, it was delivered with a certificate that specified it was grade 6082. This was the last time we ever bought key materials from unverified suppliers. The question you have to ask is; where does the aluminium come from in tools made in the far east? And is it as good as the European standard?
The great thing about using European grade aluminium and steel is the consistency you get, so that the material behaves from batch to batch. Unfortunately the trade off is cost. Quality doesn't come cheap!

Leave a comment