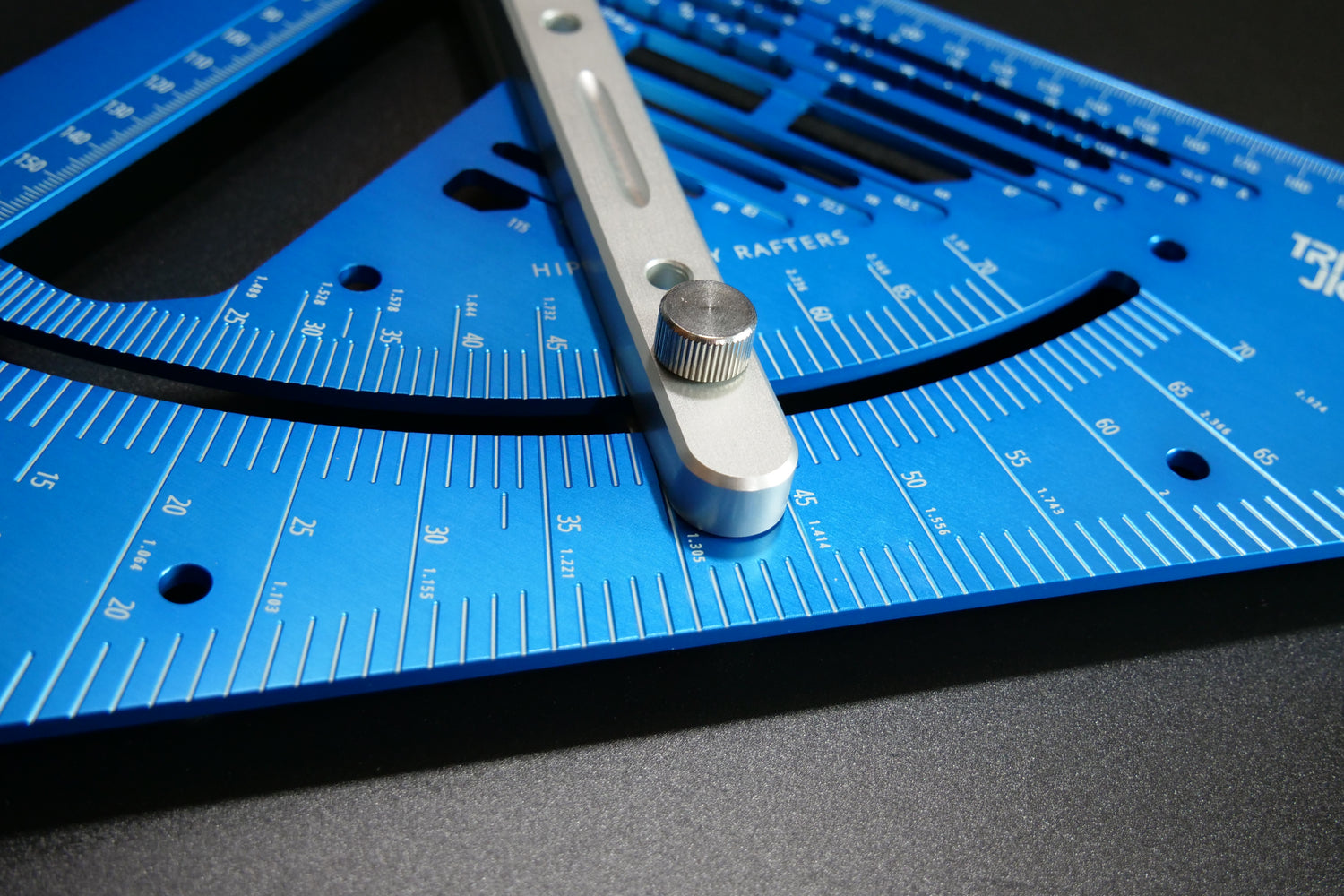
Why we make TrigJig Tools ourselves.
Since the early days of TrigJig Tools, our business ethos has changed dramatically. Thanks to the feedback from our early customers, but also through my own experience in manufacturing those first tools.
Our first tool - Digital Coving Mitre
For example; I quickly discovered that outsourcing, as a small business (i.e paying a subcontractor to make parts for us) was a great way to spoil my day. I’ve lost count of the amount of issues we had with parts that were lasered back to front, wrong way round or in the wrong material. Or vinyl graphics that were out of scale and arrived 4 weeks later than scheduled.
But I had to take some of the responsibility myself, because I was new to manufacturing and gathering experience along the journey. I was quite happy talking to the sales reps about my big ideas and what they could do, rather than discussing with the machine operatives about what they should do.

Matt and Sol, TrigJig Engineers.
We also found that buying parts from China was rarely as good a deal as first appeared. In theory, the parts we sourced from China would be the same as in the UK, but made cheaper because their overheads were less, their government ‘helped’ manufacturing businesses more and they had better economies of scale. Yes those things made savings, and they passed much of it on to us, but they also made a lot of savings using really poor materials and sometimes non-existent quality control. As a small business it’s practically impossible to return short run custom parts across the other side of the world when they don’t meet your quality standards.
So after a couple of years of trying to solve supplier issues and generally pulling my hair out, I had a eureka moment. One that most people know, but I hadn’t applied to my own business. We couldn’t make tools cheaper than the far-east, so why waste time trying? We couldn’t rely on subcontractors to make our parts reliably, so why waste our time trying? So could we make better hand tools than everyone else? Well the saying goes, if you want something doing properly, do it yourself. So I did.
How do you make the best hand tools in the world? Well, I decided to focus on the key things listed below. Today I’ll write a little about the first in my list.
- Great design
- Quality materials
- The right equipment
- Highly precise manufacturing processes
- Stringent quality control
- A clear brand strategy and values
We were confident we had the design skills in our small team. I had learned a lot after the first tools that I designed and used to launch TrigJig. We would spend hours after the working day testing design concepts, 3D printing parts and creating prototypes. Some of our ideas turned out to be damp squibs or impossible to make, and some were simple and genius at the same time, like the first Angle Finder or our ViperBite T-squares.
I discovered our ‘kind’ of customer was my ‘kind’ of person. They wanted genuinely useful tools, understood the saying ‘buy cheap buy twice’ and ‘you get what you pay for’ isn’t just a marketing exercise and applies to pretty much everything these days (after all most of our customers are tradespeople and face the same problem when their own customers want high-end work doing cheap). It’s mutual.
Some of the best designs and inventions are based on previous products, with small improvements that have big, beneficial consequences. Often you will see the same tool on Amazon, rebranded by non-descript companies. Sometimes they’re knock-offs of genuine tool designs. They’re so similar that you could be forgiven for thinking they all come from the exact same factory.
Again, this is where I wanted TrigJig Tools to stand apart as a British brand. If you see a TrigJig tool, you know it’s made by us at our workshop based in Nottinghamshire, England. If you’ve bought one, it’s quite possible, and likely, that I’ve had a part in making or assembling that specific one. What do we mean by made? That includes, design, CNC machining, blasting, de-burring, anodising, lasering, assembly, packing and even hand painting certain elements (needs a steady hand that part!) But more to come on that in an upcoming blog...
Made with the same principles where quality and pride in craftsmanship is paramount. From our workshop to yours. Take a closer look at one of our latest releases below, the MTS Micro Trim Square.
Leave a comment